MUTUAL GAINS FOR ACADEMIA AND INDUSTRY
Professor Jan-Eric Ståhl has been collaborating with Seco over two decades, feeding research results into the development of cutting-data software and training engineers in metal-cutting theories.THE PARTNERSHIP BETWEEN Professor Jan-Eric Ståhl and Seco has lasted longer than many modern marriages. For 17 years, they have collaborated in a wide range of research areas, large and small, which have had a substantial impact on Seco’s products and services offering.
Both parties see the advantages of a long-term relationship.
“The relationship with the manufacturing industry is important to me. I want to have an impact, change and contribute with my know-how and research results, while balancing this with always guaranteeing my objectivity as a professor at Lund University. That objectivity is both an asset and an opportunity for me as well as for Seco,” says Ståhl, who is a Professor at the Division of Production and Materials Engineering at Lund University, Sweden. “Overall, the purpose is to strengthen the competitiveness of Seco Tools and its customers.”
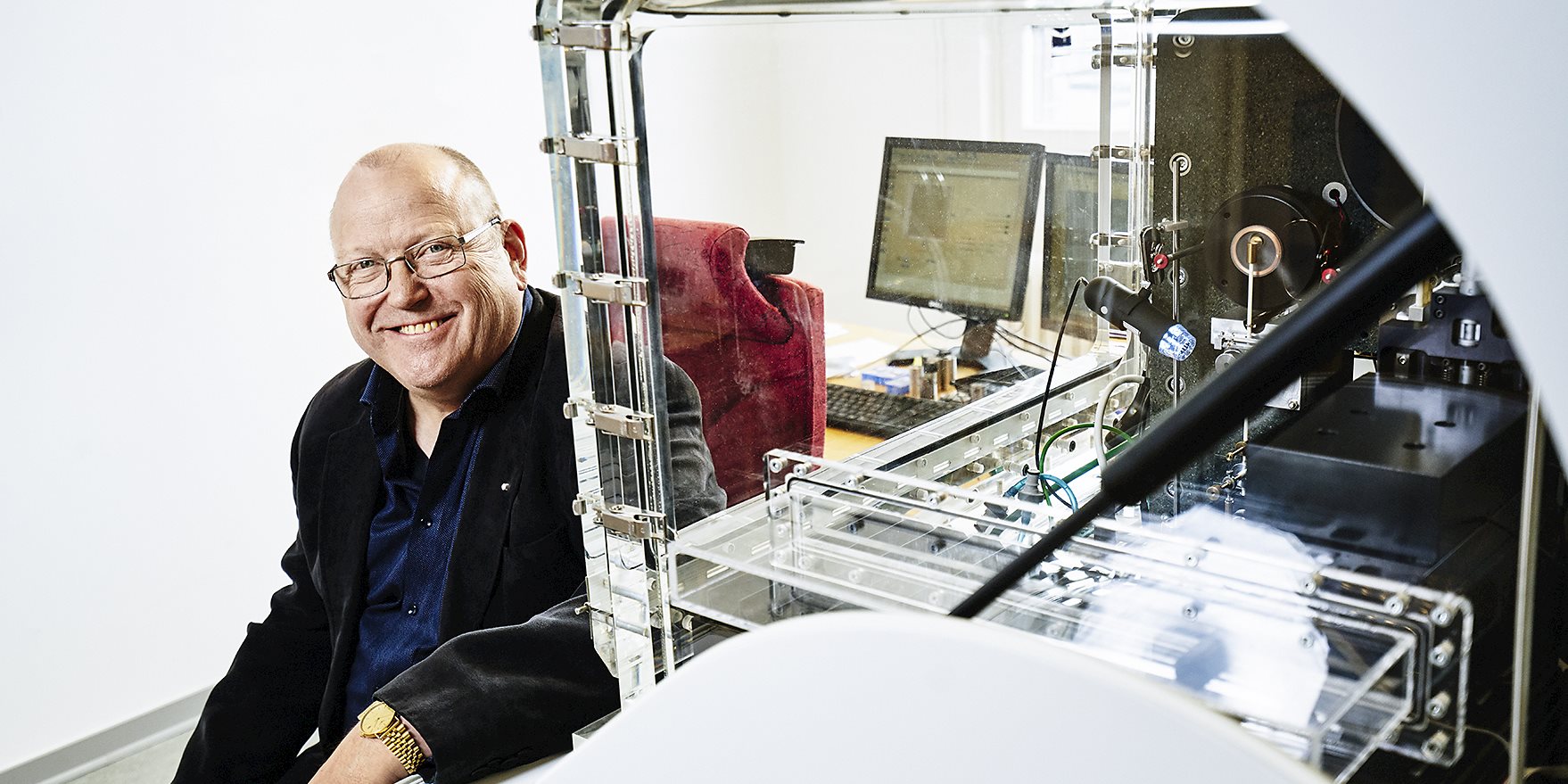
Seco certainly sees the collaboration as a fruitful one:
“The results from the research projects are very useful to us, providing knowledge that can be used in the development of our products and that can act as a basis for models to describe our products’ performance,” says Sören Hägglund, Group R&D Specialist, Cutting Data, Seco.
The first major joint project for Ståhl and Seco started in 2000 and was called ‘ShortCut’. The research team created process descriptions, explanations of how tools work and theories of cutting machining.
“We also worked with test methodology and test technology – how to perform tests in the product development process,” Ståhl explains.
Four years after ‘ShortCut’, ‘ShortCut II’ began. In this project the team focused on machinability in difficultto-machine materials, such as duplex stainless steels, highstrength superalloys (Alloy 718) and titanium alloys.
“We developed a methodology based on polar diagrams, where we look at five material properties of the workpiece material, which allows us to classify the severity of the material.”
Several of the models developed in ShortCut I and II have been implemented in Seco’s software. “It’s very satisfying that our research is used in software applications such as ‘Suggest’. Seco is a leader when it comes to user-friendliness, flexibility and the ability to use the applications in a varied way,” Ståhl says.
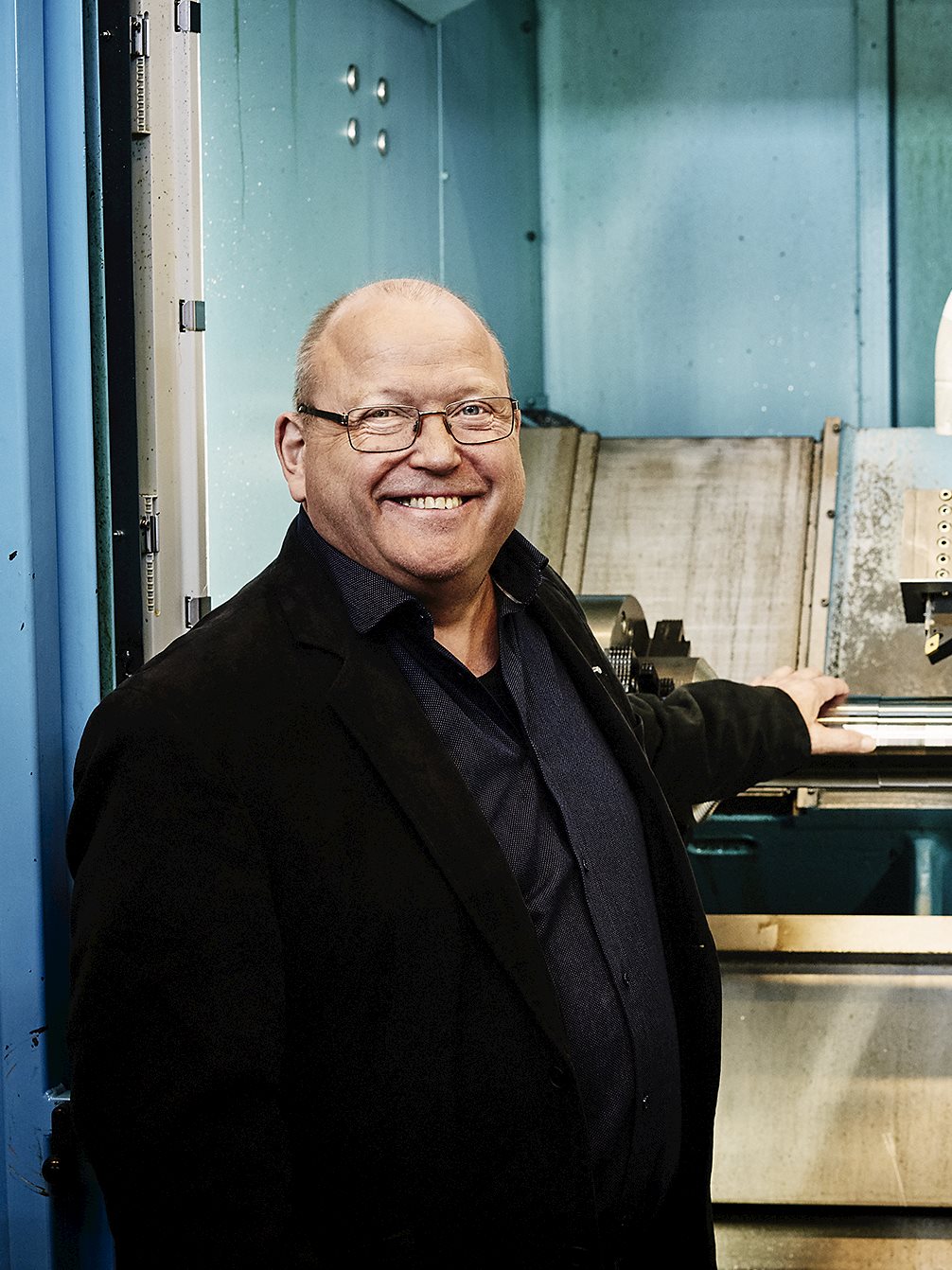
ABOUT A YEAR AGO, a big new project started that could well change the future of the whole cuttingtool business. The EU-backed ‘Flintstone2020’ project has nine partners and a budget of 47 million Swedish kronor. It aims to find the cutting material of the future, with the proviso that it must be built from non-critical commodities.
Tungsten and cobalt are the two most important raw materials when manufacturing cutting tools. In Europe they are scarce commodities, but a solution is in sight.
“We are on our way to finding new tooling concepts, built on boron nitride and synthetic diamonds,” says Ståhl, who is coordinating the project with Dr Volodymyr Bushlya, and working with research teams in Sweden, France, Germany, the Netherlands, the Ukraine and the UK.
The collaboration between Seco and Jan-Eric Ståhl extends to literature and training. In 2012, Seco Tools published Ståhl’s ‘Metal cutting, theories and models’, a comprehensive overview of the field that is widely used in Seco Tools’ educational program ‘STEP’. The book has much more life in it too.
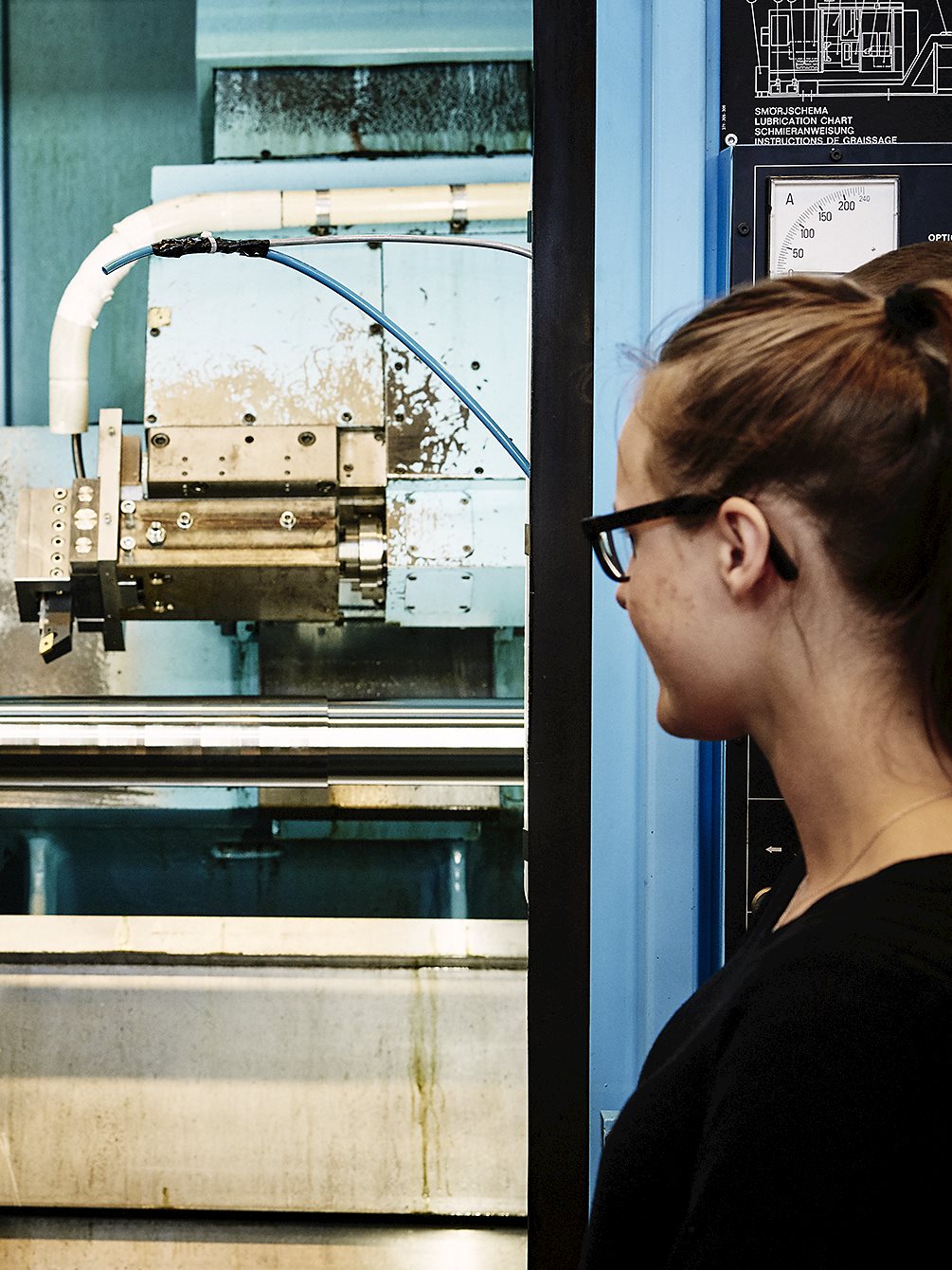
"THE PLAN IS to make a major revision of the book, but also issue a series of seven smaller books in cooperation with Seco’s Corporate STEP Educational Service Manager Patrick De Vos,” explains Ståhl. Three of the smaller books have already been published: ‘Metal cutting theories in practice’, ‘Tool deterioration – best practices’ and ‘Applied metal cutting physics – best practices’.
Over the past ten years, Ståhl has trained more than 100 engineers at Seco – operators, developers, researchers and testers – in the latest theories of metal cutting and how to put those theories into practice.
“What is interesting about cutting tools is that in most cases the cost of the tool is of minor importance while the result of the tool is prioritized,” Ståhl says. “The understanding of the costperformance ratio is vital; that is the only instrument that describes the value of using different tool technologies.”
The Lean philosophy is well established within production. It tells you to follow certain principles to obtain a good result. However, Ståhl wants to clarify the relationship between technology and economy, which he does in the production development concept ‘Next Step’. He says there needs to be a link between manufacturing processes, materials engineering and manufacturing systems.
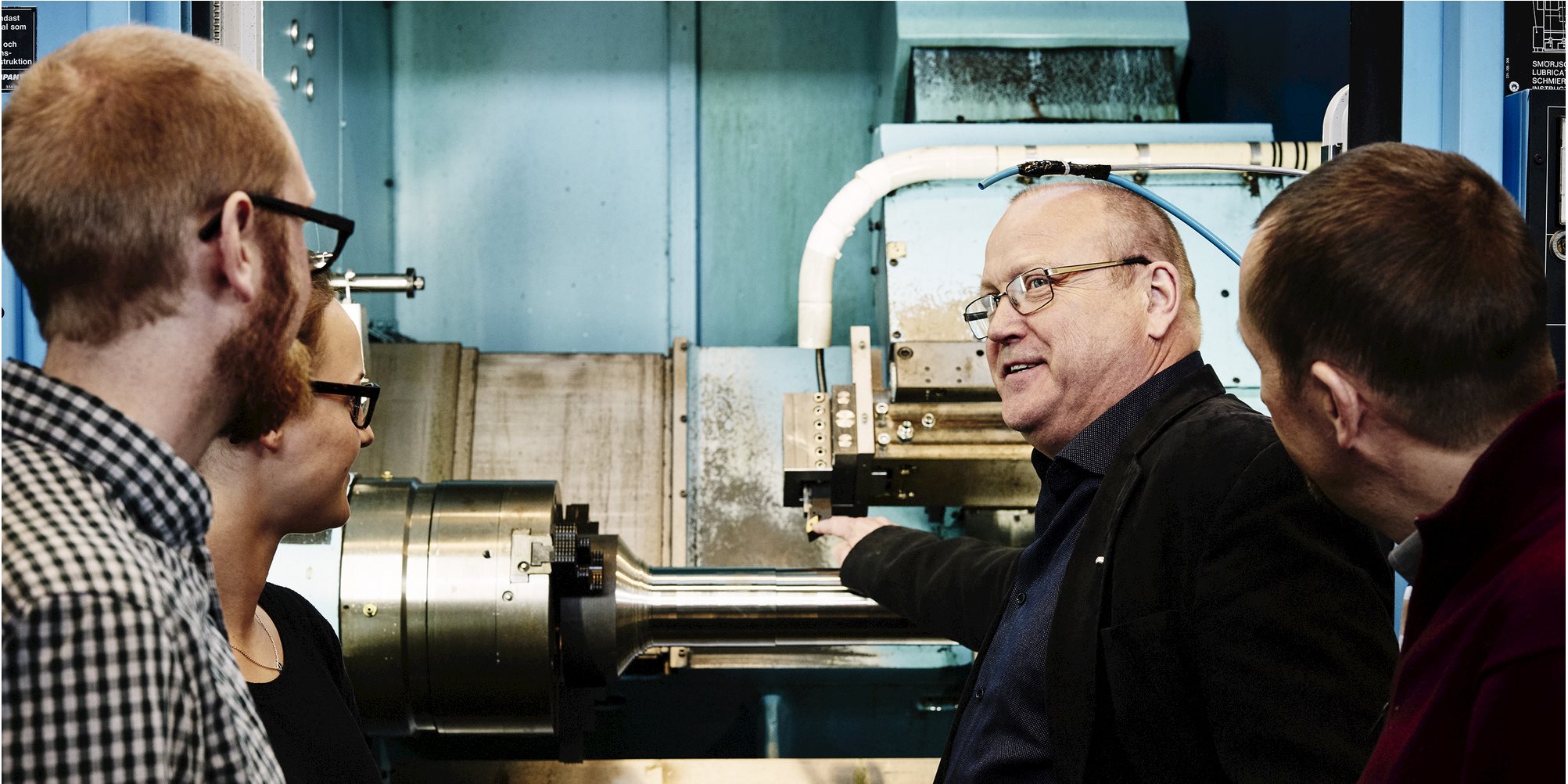
“Next Step is about putting euros and cents on technology,” he says. “We have developed a cost model to break down manufacturing costs for separate factors. This way, we can make a manufacturing economics scenario analysis that shows how a company’s competitiveness is affected.”
Despite being officially due to retire in five years, Ståhl says it takes ten years to build up the trust between academy and industry, and anticipates the partnership with Seco continuing for a lot longer.
“It’s very stimulating and interesting to work with such a successful company as Seco Tools. We will continue our collaboration for at least ten years. There are still so many things to do.”